WELDED STEEL TANKS – OUR PAST, PRESENT & FUTURE
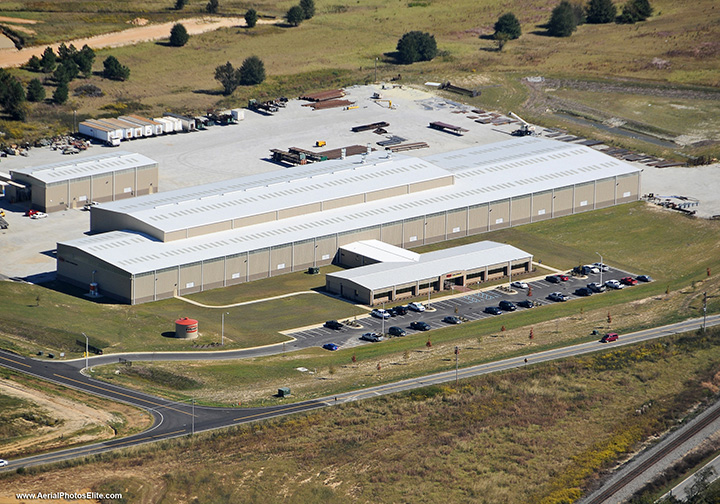
Today on the Think Tank, we’re sharing an excerpt from a 2011 article in Manufacturing Today that highlights our state-of-the-art tank fabrication facilities and offers some insight into our operations 60+ years after the company began. From our beginnings repairing storage tanks in refineries in the northeast to becoming experts in API 650 and API 620 tanks plus water storage tanks, terminal tanks, fuel tanks, food-grade tanks, and more, we have carefully expanded our reach and thoughtfully invested in equipment and technology as we’ve honed our capabilities to meet our customers’ needs. Today, as the need for crude storage and other types of storage tanks expands across the US, we are equipped to support the tank projects that will help move the US industry and the economy forward.
Excerpt from In The Tank
by Luke Gillespie, Manufacturing Today, Winter 2011
Headquartered in Chester, Pa., Fisher Tank Co. specializes in the design, fabrication, construction, repair and modification of field erected welded steel tanks. The company has two additional locations in Leesville,S.C., and Cropwell, Ala. The company was founded in 1948 and primarily serves the eastern region of the country, but will travel west of the Mississippi for larger jobs. Fisher Tank notes that while it is best known as a tank manufacturer, its repair, modification and maintenance operations have become an effective part of the company. It serves an assortment of markets, including government and military, mining, municipal, petro chemical and chemical, petroleum refining, pulp and paper, and water and wastewater treatment.
The Chester and Leesville locations are fully equipped with their own engineering, plate metal fabrication and field construction capabilities… “Fisher Tank is one of the leading full-service welded steel tank manufacturers in the country,” the company says. “We are well-positioned to provide immediate service to you.”
The company says that its in-house services are provided to customers by trained and experienced personnel that have a dedication to safety, commitment to quality and attention to schedules. “They get the job done right,” Fisher Tank says.
“We can build you a single 30,000-gallon tank, a 150,000 barrel tank, an entire tank farm, or provide you with a complete tank package including site clearing/grading, foundations, cathodic protection, painting/linings, insulation, instrumentation and much more,” Fisher Tank says.
Achieving Results
The goal at Fisher Tank is to engineer and produce safe and properly designed aboveground storage tanks that are economical for the customer. “Working together with [the customer] to achieve the best results is and has always been the Fisher Tank standard practice for 6o years,” the company says.
To provide the best possible solutions, Fisher Tank uses AutoCAD, and it says it has developed more than 50 in-house automated drawing routines that reduce the time it takes to detail during design by 50 per cent.
For fabrication, Fisher Tank relies on the long-term relationships it has developed with suppliers for more than 60 years. It explains that it is able to procure materials from various sources with the best quality and delivery, ensuring schedule commitments. “The quantity of plate material that we purchase allows us to go direct to the mills that produce the material, eliminating the middle person and saving [customers] money,” the company says. “We also carry stock material allowing us to respond quickly to our customer needs when necessary.”
The multiple locations of Fisher Tank combine to offer more than 150,000 square feet of fabrication space. “We have extensive fabrication capabilities at these facilities, with modern and efficient equipment, including plate rolls, angle rolls, CNC plasma cutting tables, gantry cutting system, various overhead cranes, automated welding and much more,” [the company] says.
Safety Priority
Safety always comes first at Fisher Tank, and the company notes that its priorities are safety, quality and productivity – in that order – and it is what [Fisher Tank] lives by on each decision it makes. “This philosophy applies to all aspects of our work from design and fabrication through the work per formed in the field and all employees from the CEO to welders in the shop and field,” Fisher Tank says. ”We are not only morally and ethically obligated to ensure the safest work environment for our employees and our customers, but it also makes good business sense. We currently have some of the lowest workers’ compensation rates in the industry, which translates to lower overhead. Our safety program has drawn national attention and earned numerous awards.”*
….”Fisher Tank Company has positioned itself to meet demand, with years of industrial experience, and efficiencies working multiple-tank projects”…mt
* We’re pleased to note that since this article appeared in Manufacturing today, we’ve maintained our exceptional EMR record, and we’ve improved our already excellent safety record, even as we’ve grown our project volume and increased activity in our shops and in the field.
For more information about Fisher Tank Company’s capabilities in terms of tank engineering, fabrication, construction and repair, and the industries we serve, please visit us at FisherTank.com.
To learn more about Manufacturing Today’s print and digital publications, visit Manufacturing Today.
Click here to read more of our blogs